Additive manufacturing: Quasi-static and dynamic strength investigations of an AlSi10Mg alloy with the development of an innovative wear-resistant aluminium-silicon alloy engineered for additive manufacturing
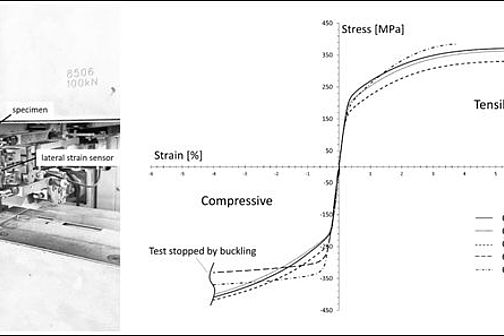
Additive manufacturing offers unique opportunities to produce complex components which are impossible or very difficult to realise using conventional manufacturing processes. The potential of additive manufacturing of aluminium alloys is already recognised in prototyping, but still holds potential in regards to the optimisation of the materials used and, above all, mass production. Due to the large growth in different areas of application, the structural mechanical properties are becoming increasingly important. The specification of anisotropies, preferred directions and weak points in the microstructure vary with the considered material, and completely opposite behaviour patterns are not uncommon. Thus, it is becoming increasingly important to gain precise knowledge about the mechanical properties of additively manufactured components. One aim of my research is to provide an overview of the mechanical properties of additively produced AlSi10Mg alloy. In particular, the influence of various heat treatments and the orientation of the components in the built environment are examined. AlSi10Mg represents the most frequently used alloy for selective laser melting followed by AlSi12. Both alloys are not optimized for additive manufacturing, as they were developed and optimized for casting. Therefore, another goal of my research is to develop an alloy, which is optimized for additive manufacturing. The AlSi alloy is develop without allying elements as they are contained in currently used aluminium alloys optimized for casting processes. Subsequently, the additive manufacturing process with integrated heat treatment is developed and optimised by using the novel AlSi alloy.